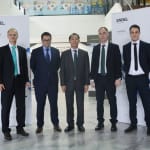
"The development of the medical technology and health care sectors in Thailand has been quite a dynamic one", reports Aram Tongurai, Managing Director of the Bangkok-based company Engel Machinery (Thailand). "This trend was in clear evidence throughout the whole event." The participants came from established companies within the industry including international companies, as well as from smaller local firms making their first moves to gain a foothold in the medical technology market. According to Aram Tongurai, there are above all two reasons for the growing interest in this industry: On the one hand, these companies are aiming for a greater degree of independence from the automotive industry, which is quite dominant in Thailand, while on the other the quality of medical care in South East Asia is steadily on the rise, in its turn leading to an increase in production volumes and shifting the focus towards state-of-the-art solutions for manufacturing processes.
From consumables to functional components
In spite of the heterogeneous knowledge base overall, all participants were able to benefit from the presentations and the components exhibition to equal degrees. Among the most sophisticated applications introduced by Gerhard Geierlehner, Sales Engineer at the Business Unit Medical of the company Engel, was the highly automated multicomponent production of drip chambers with integrated filters on a tie-bar-less Engel e-victory combi injection moulding machine, as well as the high-speed production of single-component interdental brushes with up to 500 bristles on an all-electric Engel e-motion machine. Another topic covered at the event was the cost optimisation of the mass production of components for diagnostics, such as Petri dishes, as well as highly efficient multi-component processes, which are implemented, among others, in the production of toothbrushes.All these examples showed that high-quality equipment and custom-tailored solutions are the key for achieving optimum efficiency and minimising costs per unit, while at the same time achieving high quality and a maximum of process reliability. "Especially new entrants in the medical technology sector are looking for partners capable of delivering turnkey solutions from a single source, thereby guaranteeing a high degree of overall efficiency and safety," explains Geierlehner. "And Engel is perceived as a technology leader in Thailand. It is precisely the fact that our business units have a 100% focus on one area of application that has become a strong trust factor for manufacturers, especially in the medical technology sector." The company even operates its own clean room at its headquarters in Schwertberg, Austria, the facility being dedicated to the development of new concepts for machines as well as to the carrying out of trials in collaboration with its customers.
Clean-room safety from a single source
From its production sites in Austria, China and Korea, Engel provides its customers with standalone injection moulding machines as well as highly integrated, tailor-made manufacturing solutions. Apart from the injection moulding machine itself, the turnkey production cells furthermore comprise self-developed and self-produced robots as well as individualised automation solutions, process technologies, moulds, additional peripherals as well as products which support the manufacturers' efforts of meeting the challenges presented by an age of increased digitisation and networking. The topic of Industry 4.0 is gaining in importance in Asia as well, so Gerhard Geierlehner, in his presentation, also took the opportunity to talk about the new opportunities created in this field. With its inject 4.0 program, Engel is keeping abreast of the trend by offering a large number of ready-to-market products for all areas of the smart factory environment already today.In this respect, the high degree of acceptance Engel is gaining for its ability to provide systems solutions in Asia was once more documented by the fact that some participants started discussing specific project proposals with the experts from Engel, Fostag and Hekuma while the event was still in progress.