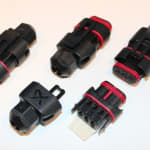
System integrator Sumitomo (SHI) Demag were one of the technology partners chosen by Molex for this entirely new manufacturing process which included two multi-cavity bespoke innovative 2-shot direct gate hot runner moulds (to make the connector cover and insert in a single mould process), management of 750 & 850 Glow wire materials with a strong bond to a second shot sealing material, plus a fast and efficient multi-component 350 tonne injection moulding machine. This would support Molex in its development of scientific expertise in materials capability relating to accurate bonding and product integrity and enable the parts manufacturer to meet initial production deadlines within 6 months of design freeze.
"We were confident that Sumitomo (SHI) Demag could provide the right equipment as they had a successful installation base of multi-component injection moulding equipment worldwide," confirms Process Engineer Donal Costello, who continues: "but more importantly we needed them to work effectively as technology partners with the other stake holders of this project. It was their extensive network of very competent and innovative experts along with their Irish based service technician and 24 hour hotline telephone support, plus their ability to help us turn this challenging project around in the short timeframe, which set them apart from their competitors."