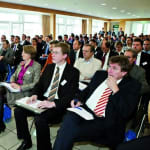
Held almost a week ago at KrausMaffei, the closing event in the SpriForm Cooperative Project attracted a large audience. Over 100 people came to Munich to find out about the latest development status of lightweight structural components.
'Lightweight structural components’ formed the electromobility-specific topic presented by the cooperative partners - Audi AG, Bond-Laminates, the Institute for Composite Materials (IVW), the Jacob Plastics Group, Lanxess and KraussMaffei - during today's closing event in the SpriForm Project. In the framework concept "Research for future production", which was financially supported by the German Federal Ministry of Education and Research (BMBF), KraussMaffei and other industrial and scientific partners jointly developed a production process during the SpriForm Project.
This production process combines the advantages of thermoplastic injection molding with the advantages of thermoforming of continuous fiberreinforced, semifinished products, so-called organic sheets, for applications in structural lightweight components. "We were delighted with the large number of persons attending the closing event", said Nicolas Beyl, Director Technology at KraussMaffei.
"The high attendance proved that we had found precisely the right topic." In addition to process development with material handling technology for the organic sheets and trim optimization for geometrically complex components, the focal point was calculation of the allplastic hybrid components. Georg Kaufmann Formenbau AG was responsible for constructing the molds.
Fiber composite technology is very important in lightweight automotive construction and the proportion of plastics as an automotive material will continue to increase. The costs and unit numbers of each component must therefore be evaluated in regard to lightweight construction potential in order to select the most suitable options from the large number of materials and production solutions.
"Due to our extensive experience in numerous production processes for lightweight fiber-reinforced components, we are a recognized partner along the entire process chain", said Beyl. "From the feasibility study through to post-mold processing and subsequent processing, manufacturers and suppliers appreciate our know-how and are increasingly asking us about interdisciplinary services."
What's unique is the extensive portfolio of processes for manufacturing composites made of thermoplastic and duromer materials containing reinforcement fibers made of glass, carbon or plastics.