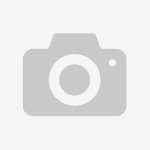
Expanding on its experience in aseptic packaging, which includes an installed base of over 200 Combis and 100 aseptic fillers, Sidel continues to innovate. Its latest development, the Sensofill FMa filler, is set for launch at the Interpack trade show in April 2008.With this new flow meter filler, sold as a standalone machine or as part of a Combi system with wet or dry decontamination, Sidel supplies the market's most comprehensive offering for aseptic packaging of sensitive products like juice and tea, flavored water and energy drinks, milk and dairy products.
Is your bottle production outsourced? Do you need flexibility for a wide variety of products or formats? The new Sensofill FMa filler is the perfect choice. Ideal for still products or products with pulp, the filler handles product and format changeovers from outside the sterile zone to ensure no loss of sterility. The system can accommodate both flat and sport caps. Internal and external bottle decontamination using high pressure jets of peracetic acid (PAA) offers the ultimate aseptic performance. Sterile water pulse-rinsing results in very low chemical residue and reduced water consumption. In addition to chemical and mechanical decontamination, a multi-wheel system treats each bottle with several nozzles, and each neck undergoes a 360° sterilization.
The newly designed, hermetically-sealed isolator and sterile air overpressure are reinforced by directed air flow in the filling zone. With this new system, bottle production can continue for 72 to 120 hours without interruption for sterilization in an environment that remains under absolute control. At the end of each run, cleaning cycles are individually optimized, with some cycles performed in background mode for greater productivity. The standardization of the operator panel with other Sidel equipment, total traceability of critical control points (CCP), and the filler's ergonomic design all simplify operation and maintenance for the user.
Is your bottle production integrated? Do you handle high volume production runs? The Combi Sensofill? FMa, which combines bottle blow molding, wet decontamination, filling and capping in a single enclosure, can guarantee top-notch production performance. The elimination of conveying, accumulation and intermediate storage and the smooth flow of bottles entering the filling zone improve your line's reliability. Transfers by the neck from the moment preforms enter the system expand the possibilities for lightweighting.
In response to your concerns about cost and the environment, the Combi Predis FMa replaces bottle rinsing with dry decontamination of preforms using hydrogen peroxide vapor (H2O2). The system reduces the number of machines and overall footprint. It guarantees decontamination without water consumption and uses only tiny amounts of chemicals.The even distribution of sterilizing agent by condensation on preform walls, the required passage of preforms through the oven, and the thermal conditioning process all guarantee activation of the H2O2. And that, in turn, ensures a 100% bottle decontamination rate for a totally secure bottle production process.
The preform infeed with dust removal using ionization and UV decontamination, the 0.01 micron filtered air used for bottle blow molding, and by-the-neck transfer of bottles under a controlled atmosphere all maintain sterility. Finally, thanks to continuous by-the-neck transfers and the absence of any thermal stress on empty bottles, the Combi solution offers great bottle lightweighting potential and total bottle shape design freedom. These solutions have been used in production since first quarter 2008. The first Sensofill FMa filler installed at Spumador in Italy is packaging isotonic drinks and fruit juices. The Combi Predis is producing juices with and without pulp at a North American bottler.