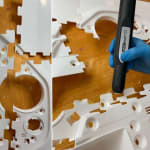
In recent years, 3D printing has become increasingly important and is now established as a manufacturing technology in both industry and the private sector. Due to its increased importance, the demands on quality, material variety and robustness are now growing accordingly. For years, the Regensburg-based company relyon plasma GmbH, a subsidiary of TDK Electronics, has been researching plasma activation in 3D printing. Creabis GmbH from Kirchheim, Germany, is a highly professional 3D printing service provider that uses plasma technology and is convinced.
A great challenge for Creabis GmbH is the 3D printing of large and complex components, since conventional 3D printers have maximum component dimensions of 600 mm. To make use of the advantages of 3D printing for larger components, they are printed as individual parts and then bonded together. In practice, predefining joint geometries with maximum bonding area and the gluing itself pose challenges that should not be underestimated. In particular, the strength of the bond is especially critical for long narrow joints where the available bonding surface is minimal.
This weakness of 3D printing is in turn the strength of the plasma technology of relyon plasma GmbH. If a surface is functionalized with plasma before bonding, the resulting bondings show a significant improvement in adhesion. This surface functionalization through plasma treatment is essentially based on two effects: Fine cleaning of the surface from organic contaminants and increasing surface energy for an improved wettability by adhesives. The piezobrush PZ2 – an efficient and compact handheld plasma device from relyon plasma that requires no special technical knowledge or complex infrastructures – is excellently suited for preparing 3D printing parts for bonding. The core of this handheld plasma device is the CeraPlas piezo plasma generator – a high-voltage discharge device for generating cold atmospheric pressure plasma.
Improved bonding through plasma activation of individual parts
Two applications of the Creabis GmbH highlight the potential of the piezobrush PZ2 in the processing of 3D printed parts. The interior door trim of an innovative small series electric vehicle of a German start-up is printed by Creabis from unfilled PA12 by selective laser sintering (SLS) in four individual parts. These are then activated with cold plasma and spotted with cyanoacrylate (superglue). About an hour later while the parts are still activated, they are structurally bonded with two-component adhesive. Dipl. Phys. Ralf Deuke, owner of Creabis GmbH, sees the use of plasma technology as extremely advantageous: ''The use of the piezobrush PZ2 now opens up possibilities for bonding individual parts that were previously unthinkable''.
This is particularly the case with the second application example, in which a motorbike fairing for racing is made from 12 individual parts using 3D printing and then glued after pre-treatment with the piezobrush PZ2. Due to the adhesive strength achieved, the fairing installed on the motorcycle can even withstand speeds of over 200 km/h. Internal tests reveal that the components treated with plasma technology have an adhesive bond that is three times stronger than that of untreated parts.
Both relyon plasma GmbH and Creabis GmbH are convinced that there are many more applications of plasma technology in 3D printing and will continue to intensify their cooperation in the future.
Source: relyon plasma