More flexibility in production thanks to mobile automation cell
At Fakuma, the new CX 160 Multinject will prove to be an impressive production cell, with compact dimensions, flexible operation and robot types that are ideally adapted to the machines. The standardized automation cell is docked on the operator rearside of the machine, particularly on multi-component machines with V units. The mobile robot cell provides high flexibility in production, and can move from one machine to the other and connect without significant effort. The core of the machine is a small robot from the Kuka-Agilus series, with a payload of 6 kg and a range of 900 mm. The main feature of this industrial robot is a high working speed and equally high precision. The integration of robot cells into the machine control system is a particularly appealing option. As with the fixed pendant installed on the machine, the injection molding machine can be operated via the handheld pendant of the robot control system. Conversely, the operator can control the automation cell via the MC6 control system of the machine. At Fakuma, a CXV 160 will produce multi-component parts from a hard polycarbonate and a soft plastic for the automotive industry.
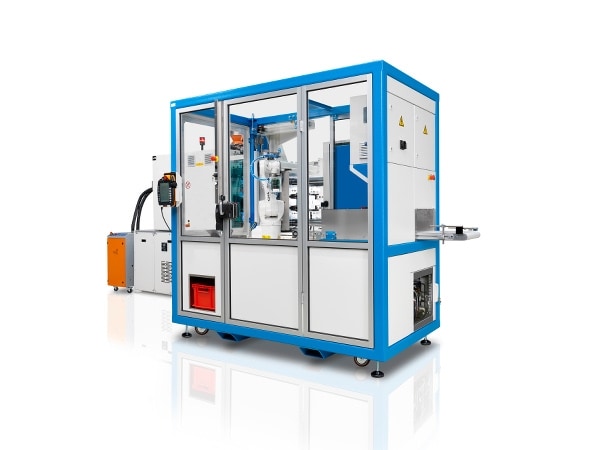
Adaptive process control system (APC) supports zero-defect production
Even in high-precision injection molding machines, fluctuations occur during the manufacturing process. These fluctuations are triggered by a wide variety of external factors, such as batch variations. This can cause the process that was initially correctly configured to exceed the defined quality tolerances, which inevitably leads to the production of reject parts. Thanks to an innovative approach to the adaptive process control system (APC), KraussMaffei has now developed a machine function that will automatically respond to fluctuations as early as the injection process. "The fact that component quality in the APC is the definitive control variable is revolutionary. The APC function allows online intervention during any cycle for corrective purposes. This opens up previously unknown possibilities for injection molding," says Dr. Reinhard Schiffers, Head of Machine Technology at KraussMaffei. The adaptive process control system automatically adjusts to the changeover point and the holding pressure profile in each cycle, which ensures that significantly fewer article fluctuations occur. This increases both function and component quality. Additional advantages: the process for dealing with interfering effects is becoming more effective. Fewer user interventions are necessary, and faster startup is possible. "Thanks to the adaptive process control system, zero-defect production is possible. Even difficult raw materials, such as mixtures or recycled material, enable consistent processing of high-quality components," says Schiffers. The APC function, which will be presented live at Fakuma, will be included on all KraussMaffei machines: all-electric, hydraulic and hybrid.
Smallest universal PU machine
The focal point of reaction process machinery from KraussMaffei at Fakuma is the new smallest size of the EcoStar polyurethane mixing and metering machine. "The EcoStar 8/8 features a pump output of 8 l/min and is ideal for first applications, simple manufacturing concepts and small series with low output rates," explains Steffen Bauer, Sales Manager for the German division. PU metering machines from the KraussMaffei EcoStar series stand out due to their high quality and low investment costs. The attractive price/performance ratio is based on consistent standardization and a reduced number of product variants. Furthermore, all the elements of the EcoStar series are engineered to very high standards to ensure a reliable and stable process and very high product quality. Just like all other types in the EcoStar series, the new EcoStar 8/8 has the same equipment as double-walled material hoppers: level monitoring, flow measurement and a Siemens S7 control system.
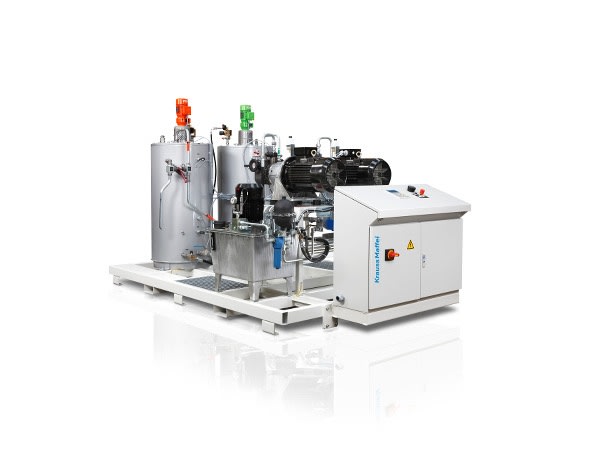