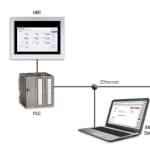
Integrated into complex control processes, the AMG is no longer a simple ultrasonic source, but instead a central, intelligent network participant within the ultrasonic welding machine. By means of control algorithms, the generator adjusts its welding parameters to the changes in the environmental conditions, allowing it to influence the weld process in a self-optimizing manner and achieve consistent product quality. Critical process states can be recognized and dealt with individually. The information is reported to the machine controllers and used for sorting out defective parts. This increases the production safety.
The ULTRAPLAST AMG offers a product platform with modular hardware versions in the ultrasonic frequencies 35, 30 and 20 kHz with a power range of 700 to 2000 Watt. It fits in all standard electrical cabinets with a depth of 300 mm. Via the new programming modules, the customer can quickly and independently use the full functional scope of the ultrasonic generator – in other words optimally control and monitor the weld process. This reduces engineering and start-up times.
Smart interfaces
For simple communication between generator and machine controller, an Ethernet communication interface (HCI Herrmann Communication Interface) is implemented in the device. This allows a fast and interference-free data and signal exchange with a manufacturer-independent PLC, i.e. a problem-fee exchange of the most important weld process data and status information. Thus advanced settings and control commandos can also be processed. If further process data and measured values are required, the ULTRAPLAST AMG can optionally be equipped with a real-time fieldbus interface. Seven of the most common fieldbus formats are supported, from Profibus and Profinet up to DeviceNet and EtherNet/IP.Diagnostics and process optimization
As a further tool, the diagnostics and operating software AMGsim is available, with which all process data can be accessed via the Ethernet network during production. The process optimization is supported by a graphical display of the most important welding parameters and makes the weld process easy to understand.Sustainability is also a part of Industrie 4.0
Ultrasonic welding is often called the green welding technology, because weld energy is only drawn for a few milliseconds and is targeted in the joining area, without any unnecessary warming of the immediate surroundings. The generation of the ultrasonic vibrations has an efficiency factor of over 88%, is not subject to any wear and does not require any maintenance. Low amounts of energy are enough to create reproducible and high-strength connections. The fully digital ultrasonic-generator is the heart of every ultrasonic welding system. To weld thermoplastic material, it must create a high-frequency electrical oscillation. This must react dynamically to process changes, but simultaneously be stable and reproducible. Only a digital generator delivers the large amount of data required for a gapless visualization and assessment of the joining process and communication for further use in the production network. Herrmann Ultraschall already developed the first marketable fully digital ultrasonic welding generator in 1997. In retrospect, the developers didn’t realize at the time what new doors into the digital age they had opened: a first but significant milestone on the road to Industrie 4.0 and the smart factory.The company will be exhibiting at K 2016: hall 11, stand E26.