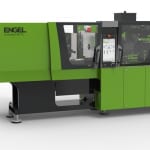
For everything from single injection moulding machines to integrated and fully automated manufacturing cells, Engel ranks as a preferred partner to the injection moulding industry in Russia. At Interplastica 2017, Engel will present a tie-bar-less Engel e-motion 170/80 TL, an injection moulding machine which guarantees very high overall efficiency, especially in the manufacture of precision parts. Design features and innovative products in Engel's inject 4.0 range both serve to achieve this.
Efficient integration of handling robots
Large mould mounting surfaces and free access to the mould area enable fast set-up processes, efficient automation solutions and compact manufacturing cells. The e-motion TL draws together these advantages of Engel tie-bar-less technology with all-electric drive technology. The machine on the Engel stand at Interplastica will produce sample parts. An integrated Engel e-pic robot will remove the parts from the mould and place them on a conveyor belt. The innovative kinematic system of the pick-and-place robot combines linear movements with a jib arm, and thus requires minimal space. The jib arm comprises a composite material which additionally raises energy efficiency and dynamism.Intelligent assistants for enhanced efficiency and quality
inject 4.0 is Engel's answer to the challenges of the Fourth Industrial Revolution. The aim is to bring about the smart factory, in which production processes continually self-optimise through the networking of production systems, the systematic usage of machine, process and production data and the deployment of decentralised, intelligent assistance systems. In this way processing firms can increase the productivity and quality of their production operations while responding to demands - which are changing ever more quickly - with maximum flexibility.To identify and automatically compensate for fluctuations in environmental conditions and raw materials, for example, Engel will utilise three assistance systems at the Interplastica event: iQ weight control, iQ clamp control and iQ flow control. Visitors to the trade show will be able to track how rejects are thereby actively avoided on the live display of the CC300 control unit of the injection moulding machine.
While iQ weight control keeps the injected melt volume consistent throughout the injection moulding process, iQ clamp control determines mould breathing in order to readjust clamping force continually.
The new iQ flow control is based on e-flomo, the electronic temperature-control water distribution system from Engel which monitors and documents all cooling and temperature control circuits linked to injection moulds and autonomously regulates either flow volumes or the temperature difference as required. iQ flow control connects e-flomo to the temperature control unit so that the rotational speed of the pump in the temperature control unit is automatically adjusted to the actual requirement. This results in greater energy efficiency. Engel developed the integrated temperature control solution in partnership with HB-Therm of St. Gallen, Switzerland; Engel has boosted its level of systems expertise with the new e-temp temperature control units.
Secure monitoring of complex processes
The use of intelligent assistance systems is a key feature of the smart factory. As processes become more complex in the face of increasing integration and networking, the means of controlling and monitoring those processes must be simplified. This is precisely where assistance systems can be used to raise process capability and quality without the machine operator needing to acquire additional specialist knowledge.With its inject 4.0 range, Engel already offers numerous sophisticated products and solutions for all three areas of the smart factory - smart machine, smart production and smart service. These generate considerable benefits both in isolation and as part of a digitalisation strategy encompassing the entire production operation.
Customer proximity ensures high system availability
Engel opened its own sales and service subsidiary in Russia in 2006. "We have managed to expand our market share in the last few years," says Olaf Kassek, Managing Director at OOO Engel in Moscow. "The field of technical injection moulding is attracting the most investment, followed by the packaging industry." With 29 employees, Engel continues to play to its strengths in Russia under the prevailing economic conditions in the country. "It is very important to our customers that we reach their premises quickly when something needs servicing," says Kassek. "That is only possible if we have the necessary manpower." Engel maintains its own spare parts warehouse and runs a special service hotline in Russia. Alongside the sales and service subsidiary in Moscow, there are two service and training centres in St. Petersburg and Nizhny Novgorod bringing Engel close to users.Engel at Interplastica 2017: Hall 2.1, stand A 25