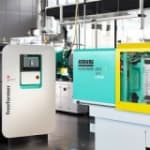
"The Fakuma will provide us with an opportunity to demonstrate that we offer our customers a truly comprehensive portfolio for efficient plastics processing," states Michael Hehl, Managing Partner and Spokesperson for the Arburg Management Team. "The eleven exhibits will give visitors a practical insight into how such product-oriented solutions can look. Key areas of industry will be represented, such as the automotive, medical technology and packaging sectors, as well as complex processes such as Arburg Plastic Freeforming (AKF), three-component injection moulding, long-fibre direct injection moulding, micro-injection moulding, Particle-foam Composite Injection Moulding (PCIM) and liquid silicone processing (LSR). Production efficiency will be the common thread running through our entire Fakuma presentation and will be the focus of each exhibit."
Individual: additive manufacturing with the Freeformer
The two Freeformers will demonstrate how plastic parts can be produced economically as one-off parts or in small-volume batches directly from CAD data, without requiring a mould. These machines use inexpensive standard granulate, building up the parts in a drop-by-drop process. This industrial process can be used to produce fully functional parts, not just demo samples and prototypes, and also enables new geometries to be achieved.The two Freeformer exhibits will have a three-axis component carrier and two discharge units, in order to produce plastic parts from two different materials. The focus will be on two-component parts and products with supporting structures that can be subsequently removed in a water bath or by mechanical means. Furthermore, the Freeformer will be integrated in the "Industry 4.0" project, which will involve the production of customised moulded parts.
Productive: around 31,500 disposable articles produced and ready-to-ship every hour
An electric Allrounder 820 A with a clamping force of 4,000 kN and a size 2100 electric injection unit will demonstrate the cost-effective production of mass-produced articles. This exhibit will show the potential of the high-performance Alldrive electric series in a high-speed application. A 24+24-cavity mould from Fratelli Bianchi will be used to produce 24 knives and forks in around 5.5 seconds, including demoulding, set-down and immediate packaging. This corresponds to an output of around 31,500 ready-to-ship parts per hour.The other hydraulic, hybrid and electric Allrounder injection moulding machines will also demonstrate a wide range of capabilities, from individual plastic parts to mass-produced articles.