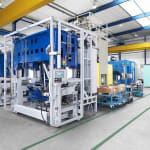
Continuous growth
In 2005 the Reaction Process Machinery department of KraussMaffei decided to build up its own mold area with molding tools and trimming technology. That is how mold toolmaking developed in Georgsmarienhütte and trimming technology developed in Viersen. Since then, KraussMaffei has been providing its customers with turnkey solutions for automotive interiors and can actively participate in the project management during the vehicle development at a significantly earlier stage. "This was the right step and is confirmed by our strong growth. We are globally present with our mold and trimming technology in all automotive markets - not only in Europe, but also in China and the US. Today, two out of three foamed instrument panels, for example, are trimmed using technologies of KraussMaffei from Viersen," states Nicolas Beyl, Managing Director Reaction Process Machinery KraussMaffei. Both locations have continuously expanded in the course of the continuously growing market penetration. Thus today there are approximately 70 employees working in Viersen and approximately 60 in Georgsmarienhütte.Viersen, the location responsible for trimming, supplies not only the conventional punch press (TrimStar), but also flexible technologies as robot-guided milling and cold-knife solutions (Routing Star). "KraussMaffei is one of the few providers on the market that can supply both variants or combinations of them from a single source. In recent years these technologies have been advanced through intensive development. That is how the TrimStar3 and Routing Star4 versions came into being," says Udo Hafer, Plant Manager Automotive Component Systems in Viersen. Currently, the ultrasonic method is being adapted to the requirements of the interior trim market. Aside from low capital expenditure, this method also features comparatively low operating costs.