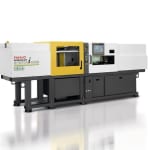
High-end Injection Moulding Applications in Two-Component Technology and Automated Manufacturing Cell
Fanuc Robomachine Deutschland GmbH will exhibit three of its electric Roboshot injection moulding machines at K 2013. These machines fulfil current user requirements aimed at low energy consumption and flawless injection moulding quality, combined with stable repeatability and maximum process security. To achieve this, the Roboshot machines are equipped with energy recovery control, torque dependent dosing control - PMC 2 and 3 - as well as with the specific backflow monitor and, finally, with efficient AI mould protection. Importantly, Fanuc proves its economic and technological competence - in conjunction with its renowned systems partners - in the areas of two-component injection moulding and manufacturing cells with the highest possible flexibility. High precision granulate mixing and dosing is controlled by motan materials management equipment.
Medical Technical applications
With a Fanuc Roboshot S-2000i-100B (1000 kN clamping force) PP closure caps for syringes are produced using a specific 48-cavity medical device mould. Parts are removed by a linear robot with a positioning accuracy of 0.01 mm, especially developed for medi
Two-Component applications
Close cooperation with Otto Männer GmbH, Bahlingen, Germany, has resulted in space-saving and economic options for two-component applications in small and micro volumes. The Fanuc Roboshot S-2000i-150B has been enhanced with an integrated rotary drive and a flexible attachment option. It has therefore been equipped with a "duo-män" bolt-on unit as second injection system. The fully electric "duo-män" injection unit is mounted directly to the mould half of the nozzle side. Using the 8-cavity 2K mould provided by Schneider two-colour felt-tip pen caps are produced in PP (16.5 grams per component) in a 17 second cycle and deposited by handling unit.