Action plan for plastic production without fossil resources
However, it is not only the European Commission working to advance the circular economy. Associations and businesses in the packaging industry are looking for their own ways forward and developing futuristic solutions. A number of weeks ago, the association of European plastics producers, Plastics Europe, released an action plan for plastics production without fossil resources. It will probably not be possible to eliminate the use of these materials entirely, but the "Plastics Transition Roadmap" shows how 65% of fossil resources in plastics production can be replaced by circular feedstocks from biomass, recycled materials and carbon capture by 2050.“The Plastics Transition Roadmap, which we developed together with Deloitte, shows how we can reduce CO₂ emissions in the plastics value chain by 28% by 2030 and transform the industry into an eco-friendly circular economy by 2050. With the support of the German government and the European Commission, European plastics manufacturers could increase the share of circular feedstocks in plastics production to 25% by 2030 and 65% by 2050.” - Ingemar Bühler, managing director, Plastics Europe Germany.
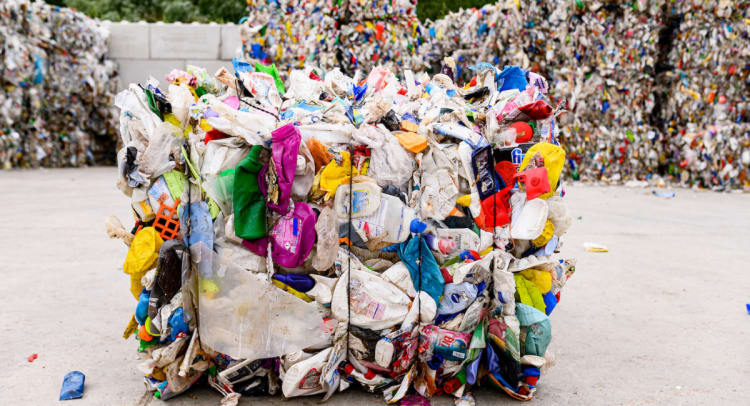
Among other things, the EU Commission’s proposal envisages reducing packaging waste by banning unnecessary packaging and promoting reusable solutions. Image: Mülltrennung Wirkt (“Waste Separation Works”) initiative/Holger Martens
Reducing plastic usage wherever possible
interpack exhibitor Greiner Packaging is also working to cut down on plastics. The packaging producer is aiming to further minimise the use of plastics with its K3 packaging solutions (cardboard-plastic combinations). The latest development, for instance, is the K3 r100. This cup’s cardboard wrap separates itself from the unprinted plastic cup on its own during the waste collection process, making it possible to recycle both materials. And there are also other solutions successfully keeping plastic content to a minimum, such as thermoformed cups, which are already labelled in the mould using the in-mould labelling (IML) process and weigh around 25% less than an injection-moulded equivalent. Another example is the company’s highly thermostable PET cups with recycled content, which can withstand temperatures of up to 120°C, making them particularly appealing for dairy products that need to be hot-filled.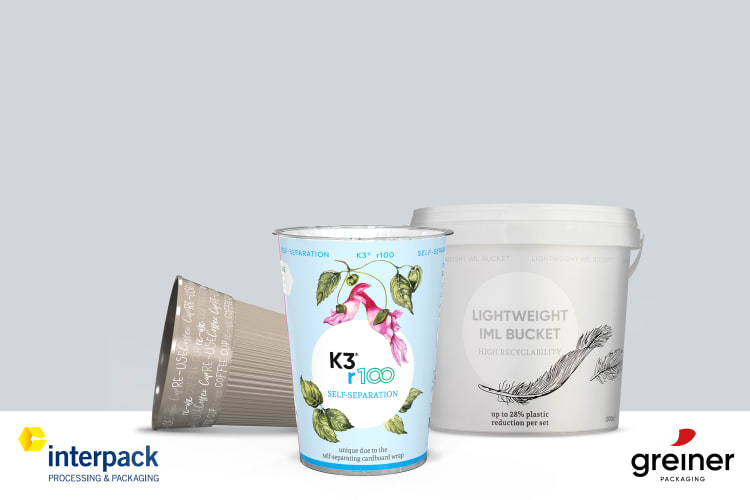
Greiner is developing sustainable solutions such as the Re-Use Coffee Cup, the self-separating K3 r100 and the lightweight IML Bucket.
Image: Greiner Packaging
Plastics manufacturers such as Joma from Austria are increasingly developing recyclable solutions that are intended to advance a sustainable circular economy by closing material loops and reducing material usage. At interpack, the company showcased a spice grinder with the “new classic” design from its re:cycle range, which is made of 100% recycled PET. rPET is currently the only plastic with a certified circular economy that is approved for direct contact with food.