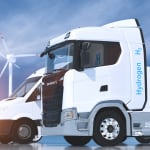
From automotive through aviation to urban mobility, industry experts and visionaries are discussing challenges and trends, new market opportunities and technological possibilities at the Engel Mobility Days 2023 – supported by KTM Technologies - in Austria in mid-June. The two-day event with top ranking keynote speakers and future-oriented machine exhibits combines and expands the previous Engel conferences trend.scaut and Lightweight Future Day to create a new networking event.
"Let's spend two days completely rethinking mobility," says host Dr. Stefan Engleder, CEO of the Engel Group, welcoming the more than 500 guests to the Design Center in Linz at the start of the Engel Mobility Days 2023. Mobility is becoming increasingly diverse and this is not only reflected in the list of participants but also in the conference programme. The keynotes will cover individual transport by car, (motor)bike or e-scooter, but also public transport by bus, train, people mover or air cab, as well as aerospace and logistics mobility solutions from the classic truck to drones. There is one thing which unites all sectors of mobility, and that is making mobility more sustainable.
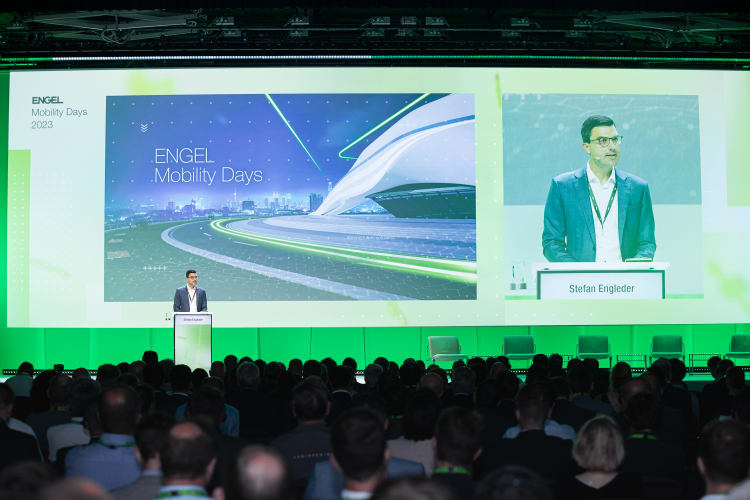
Whether new drivetrain solutions or autonomous driving, these trends are fundamentally changing the demands on mobility, requiring completely novel material and manufacturing solutions in some cases. This gives rise to huge opportunities for the injection moulding industry. "Plastics will play an even more significant role in future mobility than they do today", as Franz Füreder, Business Unit Vice President Automotive & Mobility at Engel is quick to point out. "Polymer materials are lightweight materials in themselves, and they allow for conservative use of energy and raw materials. They can be processed in a very efficient way in injection moulding, and this makes innovative technologies accessible to the mass market." The Engel Mobility Days 2023 will showcase numerous examples of this.
Autonomous driving promotes the use of plastics
Michael Fischer, Head of Business Development Technology at Engel, highlights another advantage of the material group: "Plastics are permeable to sound waves and electromagnetic radiation, and this makes them indispensable for autonomous driving." Autonomous driving is all about connectivity, communication between the vehicles themselves, and with other public and private transport users and the environment. The sensors used for this purpose rely on electromagnetic and acoustic approaches. Distance sensors, for example, work with ultrasound, while adaptive cruise control works with radar, and night vision assistance systems with infrared.
"Plastics let all of these waves through, which is why they have already replaced aluminium and steel in automotive front and rear ends," says Fischer. "Autonomous driving is a massive opportunity for plastic injection moulding. More efficient than any other method of plastics processing, injection moulding helps to combine sensor systems and electronic features with a visually appealing design."
Among other processes, Engel developed its clearmelt technology for this purpose; clearmelt is a two-component process that combines in-mould decoration (IMD) with polyurethane flood-coating. "Flood-coating with polyurethane in the mould allows for a perfectly repeatable, smooth surface with a uniform wall thickness," says Fischer: "This predestines the technology for integrating optical sensors."
BMW in Landshut uses this technological basis to produce the "kidney" panels for the BMW iX electric vehicle in a cleanroom setup. Once the radiator grille, this characteristic design feature of all BMW models has taken on a new role following electrification of the drivetrains. The kidney-shaped panels protect a series of sensors for assisted and, in the future, autonomous driving. To make sure that the sensors also work reliably in the winter, BMW back-injects a heatable functional film with polycarbonate, which is then flood-coated with polyurethane. Following several applications for the vehicle interior, this is the first time that BMW is using a combination of film back-injection and flood-coating in the series production of functional parts on the exterior, where they are exposed to particularly high stress. The sensitive electronics are well protected under the scratch-resistant polyurethane surface. The high gloss level and depth effect, which even a thin coating of polyurethane achieves, convey a very elegant impression. Engel is the system supplier for this demanding project. The production cell integrates an Engel duo combi M injection moulding machine with a horizontal rotary table, two large articulated robots for handling the films and moulded parts, a film cleaning system, an inline quality-control station and peripheral units including the polyurethane feed.

The kidney-shaped badges for the new BMW iX are produced in a highly integrated cleanroom production cell by Engel. This is the first series production application for combined film back-injection and flood-coating with polyurethane on the demanding vehicle exterior. (Picture: BMW Group)
Engel is collaborating with development partners in the field of combined back-injection and PUR flood-coating, including Leonhard Kurz Stiftung, Schöfer and Votteler Lackfabrik. In the scope of a project study, the partner companies were able to demonstrate that flood-coating with polyurethane, which is equivalent to in-mould painting in terms of the process, accounts for only 20 percent of the total energy consumed in the production process. This means that the integrated process offers significantly improved energy-efficiency compared with painting the parts outside of the injection moulding process.