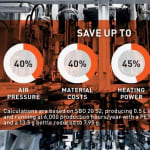
"By keeping the use of PET material to an absolute minimum and doing the same with consumption of electrical power and compressed air, Sidel can help beverage producers to make significant savings, minimise running costs and achieve a very fast return on investment (ROI)," explains Samuel Le Guen, Global Maintenance and Line Improvement Director at Sidel. "When it comes to energy efficiency, the blower often offers the biggest opportunity for improvement, accounting for up to 70% of the total line power consumption," he adds. "In recognising this, we have leveraged Sidel's extensive experience in blow moulding technology to develop our comprehensive ECO Booster service."
Improved monitoring and greater awareness
The ECO Booster portfolio comprises five modules. The recommended starting point is the ECO Audit performed on the customer's blower to analyse production conditions and energy consumption. The ECO Audit provides clients with a customised report including an outline of potential gains and predicted cost savings in electricity, heating and air consumption costs.Upgrades to reduce consumption
The ECO Process module provides carefully calculated adjustments and process improvements proposing specific upgrades. The ECO Heating module involves the optimisation of the heating profile with less installed power: available options like the ECO Oven, ECO Lamps and ECO Oven Top Reflectors optimise the blower heating performance to achieve up to 45% electrical consumption reduction. Additionally, the ECO Air module reduces the electricity consumption through the installation of an Air Recovery Kit, leveraging on re-use of up to 40% compressed air during production.Lightweight design with heavyweight performance
While reducing the consumption of both electricity and compressed air during the blowing process, Sidel's expertise in optimising the bottle design can also bring its own benefits. The ECO Packaging solutions enable producers to transform the shape of their packaging while improving its appeal, performance and safety. With more than 35 years of experience in PET packaging, Sidel can assist beverage customers in achieving more from the production process by reducing the use of PET resin. By saving just one gram on a 0.5 litre PET bottle, overall savings of EUR 350,000 per year can be generated. One step in making these savings in PET bottle production is the reduction of the neck height. Soft drinks bottles can have neck heights reduced to as little as only 12 millimetres high.Two packaging innovations can easily demonstrate the company's ability to solve the dilemma between lightweight PET design and the need to protect the brand experience in the hands of consumers, all without compromising on production costs. Bottles designed following the Sidel RightWeight concept can offer improved performance and reductions in material costs, while the implementation of the Sidel StarLite base in PET bottles will enable a reduction in air blowing pressure, yet increase the resistance of the base and stability of the bottle.
Weighing just 7.95 grams, the RightWeight 0.5 litre concept bottle is around 34% lighter than the average commercial bottle for still water and demonstrates an impressive top load performance of 33 kilograms - 32% more resistant than the lightest commercial bottle. Not less important, the RightWeight bottle achieves this rigidity without the use of nitrogen dosing, again minimising costs. Utilising two proprietary PET design innovations, the Sidel StarLite PET bottle base for still drinks has a unique shape that makes the bottom of the container significantly more resistant and stable. Additionally, it offers better protection against extreme temperatures (hot and cold) while reducing energy consumption during production, lowering package weight and improving design flexibility - all without compromising on bottle integrity or product safety.