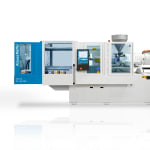
All-electric AX machines with high energy efficiency
All-electric AX series injection molding machines from KraussMaffei feature resource-efficient manufacturing with high repeatability. They earn a rating of Class 9+ on energy efficiency tests. "Compared to similar hydraulic injection molding machines, energy consumption is reduced by 50 percent or more," explains Jochen Mitzler, Head of Strategic Product and Technology Management at KraussMaffei. At Fakuma, the smallest all-electric production cell, an AX 50-180, will demonstrate injection molding that is extremely precise and energy efficient by manufacturing a soap stick container made of polystyrene. The optimized 5-point toggle design, efficient servo motors and the easy action of its mechanical systems guarantee the optimum efficiency of the machine. A flow monitoring system integrated in the MC6 machine control system for the cooling/temperature control water makes a contribution towards zero-defect production and documents the process values of mold heat-balancing. The AX series therefore offers optimum prerequisites for efficient and precise manufacturing. It lets the processor produce flexibly, reliably and, above all, at low unit costs.An additional step in reducing unit costs is the use of CellForm technology, which reduces component weight through physical foaming and simultaneously increases dimensional stability. Interested visitors can visit the booth at GWK (Hall B1, Booth 1205), where they will be impressed by a KraussMaffei AX 130-750 CellForm with an integrated LRX 50 linear robot that produces foaming components with high-gloss surfaces. "This is made possible through the use of dynamic mold heat-balancing. A design suitable for use with MuCell provides up to 35 percent material savings," says Mitzler. The AX machine exhibited at Fakuma is equipped with the new MuCell system. It is particularly easy to operate because all parameters are integrated into the MC6 control system and, thanks to a new dosing unit, it is very compact.
CX 80 Hybrid reinforces functional integration
Functional integration is the buzzword for the Blue Competence campaign initiated by VDMA at Fakuma 2014, in which KraussMaffei is participating. At the KraussMaffei booth, a CX 80 Hybrid will demonstrate how strip conductors with press and hold functions can be integrated directly into a thermoplastic component. The IMKS procedure is used for the two-component part (integrated plastic-metal injection molding). The metal injection unit adapted for this purpose by the KraussMaffei mold partner Krallmann can be positioned particularly well in the large mold area of the CX machine. The smallest KraussMaffei linear robot, the LRX 50, removes components through lateral mounting and storing within the standard protective enclosure. "The standard protective enclosure of the machine serves as a robot safety fence, which saves approximately 100 percent of the installation area used for conventional automation," says Mitzler.The basic principle of the CX Hybrid series is a combination of the advantages of the space-saving hydraulic clamping unit (twin-plate technology) with those of the electrically driven injection unit. This unit features high precision injection and is able to plasticize during the mold movement. The new BluePower drive, in combination with the hybrid injection unit, reduces energy consumption in spite of its high power density.