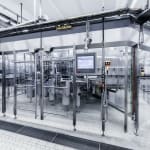
Smart systems which save energy and resources: from November 12 to 14, 2019, KHS is exhibiting intelligent beverage filling technologies at the BrauBeviale trade show in Nuremberg, Germany. One example of the above is the new high-performance KHS glass filler with a capacity of up to 80,000 bottles per hour. With it the German systems supplier is helping the beverage industry move towards more efficient, more sustainable and increasingly digitized beverage production.
In November the international beverage industry will again meet in Nuremberg. At this year’s trade show KHS’ main focus will be on process efficiency, digitization and saving resources. “The entire production process is becoming increasingly smarter. As a trusted and reliable partner to the beverage industry we’re applying our extensive experience and line expertise to cater for this development,” says Dr. Johannes T. Grobe, CSO of the Dortmund machine and systems manufacturer. “At BrauBeviale we’re thus presenting intelligent technologies which will map out the direction KHS will take both now and in the future.”
Considerable savings in energy and resources
One example of this is the new generation of glass bottle fillers KHS will be showing to the public for the first time at the exhibition. With it the turnkey supplier is consistently advancing its aim of continuously reducing the amount of energy and resources consumed within the beverage industry. Among other features the filler has a unique ECO system and special evacuation and CO2 purging process for glass bottles. With this the system uses up to 50% less CO2 compared to conventional methods. KHS has also cut energy consumption by a maximum of 20% thanks to its optimized vacuum pump. “The protection of the environment is one of the determining issues of the moment. We thus offer our customers systems which specifically make their production lines sustainable and efficient,” explains Grobe.
Smart KHS systems noticeably optimize production processes
Here, an important role is played by smart engineering which noticeably simplifies, optimizes and automates production processes. To quote one example, a diagnostic assistance system monitors the entire filling process with regard to the evacuation and CO2 purging processes, for instance, to considerably minimize the amount of oxygen pickup. Broken bottles are also detected in all filling phases and the containers automatically channeled out of the system. “We’re constantly improving the efficiency of production processes. This in turn brings about a clear improvement in the line performance,” Grobe states.
Sustainable in every respect
In the future, too, one of KHS’ prime concerns is to significantly reduce our carbon footprint. Service plays a central role in the persistent pursuit of this goal. KHS enables its customers to operate systems for as long as possible and keep them in line with the latest technical, economic and ecological state of the art. Its bottle washing machine optimization program is exemplary in this respect. This aims to successively lower the amount of water and energy the bottle washers use.
In this context the Dortmund engineering company provides various smart service packages from the capacity-dependent fresh water controller to weight-optimized bottle pocket carriers. “We take a holistic view of our customers’ production and maintenance processes. With our extensive service program, including line optimization measures to boost efficiency and throughput, together we find the best possible solution and in doing so also help protect the environment,” declares Grobe.
Source: KHS