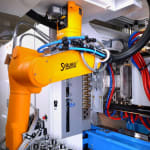
The higher the level of performance, the higher the effort for the fine-tuning. It is no difference in the interaction between high performance injection molding and handling automation. In order to keep the qualification steps for high performance in serial production as short and efficient as possible, the southern German Hekuma GmbH offers a new "training system", which enables the manipulation speed of the series production to be driven in trial run, without the requirement that the serial peripherals be already available.
The HekuCell is a flexible deployable automation cell for product sampling, pilot run production, and system testing under high speed conditions, for example as in product development or for the production of validation samples.
It is designed as original equipment or for retrofit on high-speed injection molding machines up to 2,500 kN clamp force and contains a fast six-axis industrial robot as a major component. Beyond the use for system testing, the HekuCell concept also offers potential for upgrading of injection molding productions of all kinds, such as free-falling de-molding and for retrofit wherever a 3-axis linear unit does not come into question due to limited space.
The high performance automation of fast cycling injection molding systems has achieved a level, with removal times of less than 0.45 seconds, even with multi-cavity tools and overall cycle times of significantly less than 5 seconds, at which all system components must be fine tuned to the actual feasible limits of each other.
This tuning and process optimization begins with the product design and continues through the mold function, to the sequence optimization in the handling periphery, up to the pilot run production of a series for product validation. Inherent are sufficient testing and qualification phases necessary, as near as possible to the actual production conditions. Normally, as the series production facility is not yet available in this project phase, an inexpensive replacement with comparable performance is needed.
The southern German automation specialist Hekuma, a provider of high performance removal and assembly equipment for high-speed plastic part production, presents a high-performance cell, which was specially designed for testing, qualification, and pilot run production under simulation of production conditions. It is the "HekuCell", which can be combined with any standard horizontal injection molding machine with up to 2,500 kN clamp force (Ill. 1). It consists of an industrial robot, a gripper for removing the molded parts, its own sequence control, and a protective cell.
The characteristic feature of HekuCell is the performance of the implemented 6-axis articulated arm (industrial robot) for the handling of parts (Ill. 2).
It combines two advantages in one device. On one hand, the robot can score points with fast movements and is therefore ideal for the simulation of "real" high performance handling tasks, on the other hand, the articulated arm concept allows a parts transfer in a confined area, similar to the conditions of mass production, even with large end of arm tooling for take-out with multi-cavity tools (Ill. 3).
Typically, the automation module is docked to the rear of the machine. The control cabinet is integrated into the cell and is connected to the machine control through a Euromap interface. Setting up the movement sequence of the six-axis robot is very easy and comfortable with a self-explanatory teach program, which is operated by a control panel.
The HekuCell is designed as a modular system and can be easily adapted with modules, such as conveyor belt, tool carrier transfer system, or simply with transfer stations. Optionally, it is possible to expand the base cell with other modules. These include inspection, assembly, or packaging stations.
The HekuCell is not exclusively used for sampling tasks or pilot series productions, but also offers advantages for special application niches in standard injection molding. For example, wherever a "top-entry 3-axis linear robot" can not be used due to the low ceiling height. In the HekuCell, which is designed exclusively for lateral part removal, no robot component extends beyond the protection of the cell or machine height, neither at rest nor in motion.
Since each HekuCell is barely wider than a conveyor belt, it is even more advantageous when handling units are to be retrofitted into existing production systems with small distances between machines.
Hekuma sales manager Klaus Wanner concludes: "With our new HekuCell we offer an entry-level option for all applications where system components for high-volume production systems must be developed, tested, and qualified under realistic conditions, which is usual in medical and electronic industry practice.
The applications range from product development, to the test tool, or the pilot production for the product validation. A particular advantage is its flexible application. The HekuCell can be converted quickly to a new product. If necessary, it can be expanded up to a production cell. In addition, this compact cell concept also provides potential for upgrading quite "normal" injection molding production with free falling injection molding products, or when a top-entry 3-axis linear robot is not an option because of the low ceiling height."