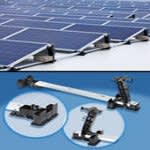
The plastics processor Ensinger located in Nufringen, Germany and BASF have entered into a joint undertaking with the Goldbeck Solar company to develop a modular mounting system for flat-roof solar installations in which the load-bearing elements are made of a BASF engineering plastic for the first time. Thanks to the new system, solar panels can be installed on flat roofs more easily and more quickly. The lightweight material employed here is Ultramid, a member of the chemical company’s polyamide product line. The entire substructure comprising support elements made of plastic and stamped metal parts was recently launched onto the market by Goldbeck Solar under the brand name SUNOLUTION. The first customer project was a 300 kW system that went into operation in the Aschaffenburg area in October of 2012.
Easy to install – light in weight – gentle on the roof – highly integrated
The advantages of the new support elements made of this application-optimized thermoplastic include especially the fact that the roof membrane is not punctured or damaged during the installation work. The roof remains water-proof without the need for any additional sealing measures. Moreover, Ensinger was able to benefit from injection molding of thermoplastics, integrating numerous functions into the plastic structure. In a single manufacturing process, Ensinger has incorporated snap-on connections, ribs and cutouts for draining the water and laying the cables. All of this resulted in parts that are very lightweight and easy to mount. Up to now, substructure systems for photovoltaic installations on flat roofs had been made primarily of steel and aluminum.
Computerized weather-proofing
The plastic Ultramid lends itself optimally for use in outdoor applications since it has a very low tendency to creep, even at high temperatures (up to 80°C [176°F]), and since it exhibits extraordinary toughness and stiffness all the way down to temperatures of -30°C [-22°F]. Moreover, this highly fiberglass-reinforced polyamide is UV-resistant and weather-resistant. It is one of the engineering plastics that has successfully passed the battery of tests involving outdoor exposure and for which a life service of 20 years has been substantiated in accordance with ISO 4892-2 Cycle No. 1. BASF’s own computer-simulation tool Ultrasim® made it possible to optimize the components to meet photovoltaic-specific requirements such as exposure to snow and wind loads, and to achieve a low intrinsic weight.
Simple mounting system for cost-effective installations
The substructure consists of very few individual parts: two identical pedestals made of plastic are joined together by a metal rail. A plastic bracket is mounted vertically on the rear pedestal by means of a snap-on connection and simple screw elements. In this manner, the front pedestal and the plastic bracket form the contact surface for the PV module, providing an ideal angle for incident sunlight. The dual function of the pedestal not only simplifies the installation but also reduces logistical effort and thus fixed costs.
The development of this substructure is yet another way in which Goldbeck Solar can continue to offer cost-effective solar installations to its customers. Particularly the consumption of self-generated solar power will acquire ever-greater significance for industrial customers.