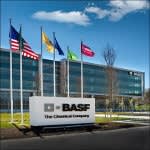
In the air intake region of the charge-air manifold, which features integral exhaust gas recirculation, fresh air and hot exhaust gases are brought together. This is where high mixing temperatures and strong turbulence are encountered. Until now, an aluminum shield provided protection for the wall and a built-in sensor. Now, a heat-resistant plastic insert fulfills this function. The special heat aging resistance of Ultramid Endure comes into play here: The material easily withstands a continuous service temperature of 220°C and peak temperatures of 240°C. Stabilization technology that creates a protective surface layer on the plastic is responsible for the high heat resistance of this polyamide specialty.
Perforation for favorable flow
Two additional properties of the plastic distinguish the new heat shield from its metal predecessor: First, the plastic functions as a thermal insulator. Additionally, it was possible to incorporate openings in the Ultramid Endure heat shield to produce a specific turbulence in the charge air. Moreover, the weight of the plastic part is only half of the previously used aluminum part.
High-temperature resistance versus system costs
The engine compartment is becoming increasingly compact and thus hotter. At the same time, the vehicle should become lighter by substituting plastic for metal. Because of their high system costs, however, high-performance plastics are ruled out. The new polyamide Ultramid Endure combines its exceptionally high heat aging resistance with the good processability of PA66 – the characteristic that is the determining factor when it comes to system costs. The material is thus an ideal alternative for applications all around the charge-air system in modern turbocharged engines. Thanks to the design freedom that the injection molded plastic provides, the automotive supplier can address the individual requirements of a vehicle manufacturer specifically.