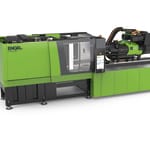
Engel is increasing its customers' competitiveness with tailor-made production solutions. The efficiency of the injection moulding machine is a key factor in the cost-effectiveness of the application. At K 2019, from October 16th to 23rd in Düsseldorf, the Engel e-mac 280 is taking to the packaging floor, allowing for an even more granular performance gradation for the packaging industry in all-electric use cases.
Tube collars made of HDPE (Borealis Borouge) with a total shot weight of 81.6 grams are being produced on an all-electric e-mac 740/280 injection moulding machine, using a 48-cavity mould by Sibo. The cycle time is eight seconds, and therefore precisely in the range in which the e-mac plays out its efficiency benefits to the max. “The e-mac combines very high energy efficiency and precision with a particularly compact design and comparatively low investment costs,” as Friedrich Mairhofer, Product Manager Electrical Machines at Engel stresses.
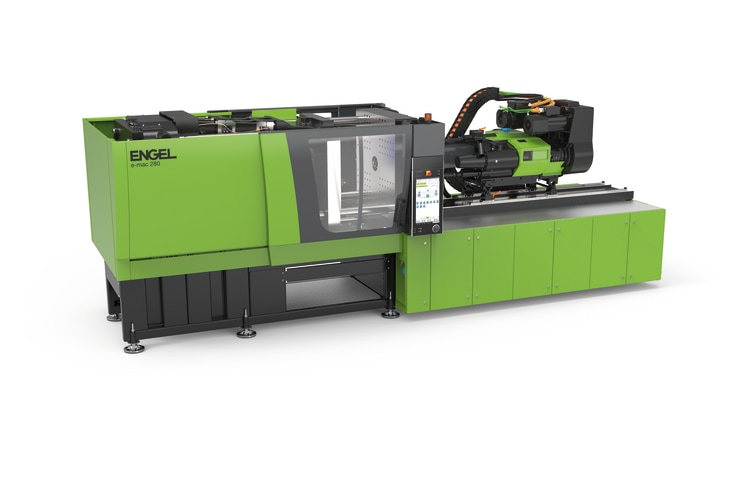
With their excellent energy efficiency, precision and compact design, the all-electric e-mac injection moulding machines are used in a wide range of applications
Compact machines for higher productivity per unit area
Using an optimised toggle-lever design, the clamping unit of the e-mac 280 is particularly shorter without reducing the opening stroke. “This makes it possible to leverage shop floor space to the max and increase productivity per unit of area,” says Mairhofer. As a result, the e-mac 280, with its clamping force of 2800 kN, is often found in applications with large multi-cavity moulds.
The Engel e-mac machines are exclusively equipped with particularly powerful servo-motors, including the ejector and nozzle movement. This not only ensures maximum precision and process stability, but also an optimum overall efficiency level. “With its performance features, the e-mac is the most cost effective solution for many packaging applications with a cycle time of more than six seconds,” says Mairhofer. All told, the series covers a wide spectrum of applications. Featuring clamping forces of 500, 750, 1000, 1800 and 2800 kN, the e mac machines have become very well established in the teletronics and technical moulding industries.
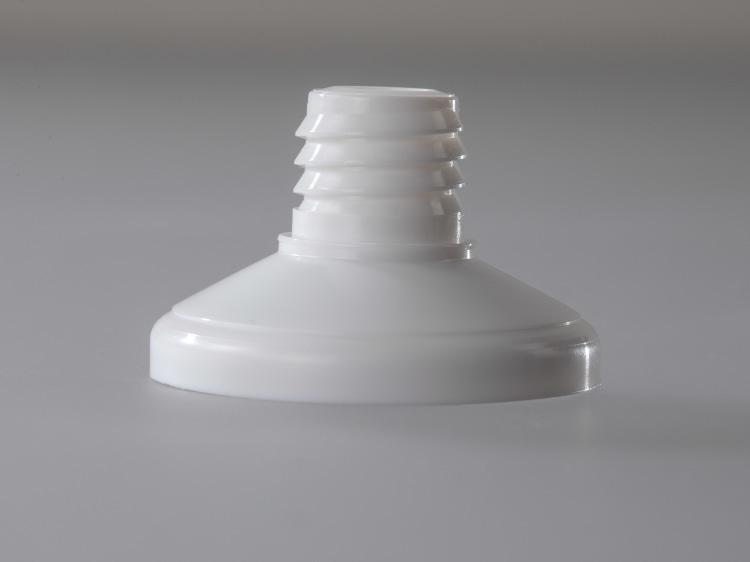
Engel is producing tube shoulders made of HDPE on an all-electric e-mac injection moulding machine at K 2019
Two series for even shorter cycle times
In the high-speed, all-electric high-performance range, with cycle times of less than six seconds, Engel's e-motion series and e-cap machines, which are tailored to caps and closures applications, meet a wide range of market requirements with the highest precision and cost-effectiveness. Together, the two series cover a clamping force range from 300 to 6500 kN and achieve cycle times of less than two seconds. Both the e-motion and e-cap machines are equipped with encapsulated toggle levers and a very clean linear platen guide; this makes them ideal for strictly regulated production areas and cleanrooms in the foods and medical technology industries.