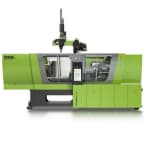
Efficient use of LIM multicomponent processes
The main demands as regards the processing of liquid silicone (LSR) are that it must be fully automatic, waste-free, low in burrs and require no reworking. An Engel e-victory 200H/80W/120 combi injection moulding machine – automated with an Engel viper 20 linear robot – will impressively show that Engel system solutions not only meet these requirements fully, but also handle LIM multi-component processes securely and efficiently. A mould provided by ACH solution (Fischlham, Austria) will be used to produce sensor housings for flow measurement with integrated seals. Engel can guarantee maximum precision by using servo-powered injection units. Normally the LSR field requires special solutions where very small injection unit volumes are involved. In this case Engel meet that need with a standard unit. Developed and patented by Engel, iQ weight control software applied in the system recognises and automatically compensates for fluctuations in melt quantity during the actual injection process.The tie-bar-less technology of the Engel e-victory machine also makes a decisive contribu-tion to high process stability in this application, while the patented force divider evenly introduces force to the mould across the platen face. Both outer and inner cavities are thereby kept closed with precisely identical force, significantly reducing mould wear and raising prod-uct quality. On top of this, free access to the tie-bar-less machine's mould area facilitates the most effective automation concepts.
All-electric for maximum performance
500 ml food containers will be produced on an all-electric Engel e-motion 440/160 featur-ing a 2-cavity mould by Glaroform (Näfels, Switzerland). In-mould labelling (IML) will be used to decorate the packaging; to do this, Engel will collaborate with partner company Beck automation (Oberengstringen, Switzerland).The steady enhancement of the Engel e-motion series is serving to establish the machines in the field of high performance applications for the packaging industry. The newest machine generation is able to achieve cycle times of well under three seconds and injection speeds of more than 500 mm per second, thereby combining maximum performance with maximum energy efficiency. The closed system for toggle lever and spindle always guarantees optimal, clean lubrication of all moving machine components. This makes the Engel e-motion the preferred machine type even in regulated areas such as food packaging production.
Maximum reliability with excellent efficiency
Using the example of a medical technology application Engel demonstrates how maximum efficiency can be reconciled with maximum process reliability. An all-electric Engel e mac 440/100 injection moulding machine will be manufacturing polystyrene needle holders for safety hypodermics using a 16-cavity precision mould by Fostag, Stein am Rhein, Switzerland.In order to transfer the specific requirements of the medical technology industry, such as maximum product safety, absolute cleanliness and precision as well as full documentation, to efficient injection moulding processes, Engel dedicates an entire business line to this industry. On the basis of its in-house clean room and a series of resulting machine concepts for clean room use, the injection moulding machine manufacturer has acquired extensive experience in the medical field and competence with clean rooms.