Precision and efficiency for liquid silicone rubber
On a fully automated high-end production cell Engel produces blade valves made of liquid silicone rubber (LSR). A seamless integration of tiebarless injection moulding machine, peripherals, automation and digital solutions ensures quality and at the same time high efficiency and cost effectiveness. Whether in cars, medical technology products or packaging, blade valves are used in a very wide range of applications. What all of these applications have in common is the very strict process consistency requirements in terms of injection moulding production. The precision of the small parts is safety-relevant.The production cell at the Engel stand leverages the quality and efficiency potential for the production of blade valves with a blade diameter of 7 mm in the best possible way. It combines an e-victory injection moulding machine and smart digital assistance with Nexus's innovative mould and plasticising technology. Production is fully automated in a 64-cavity mould with an Engel easix articulated robot and an integrated vision control system for 100 percent quality control.
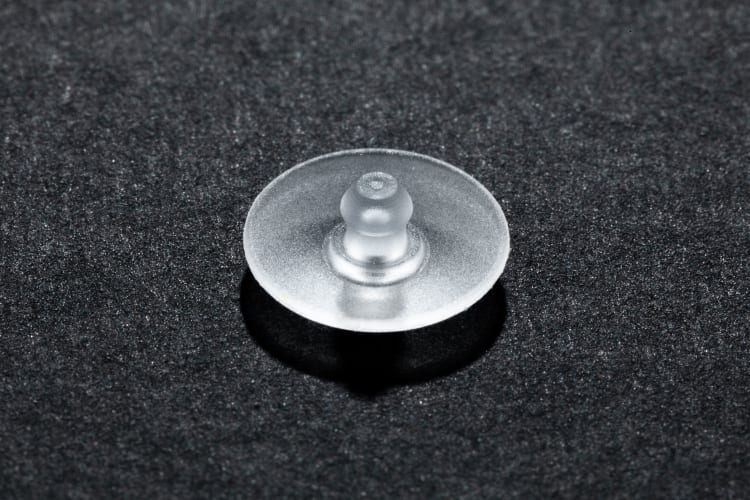
LSR blade valves are important components for functionality and safety in many applications. The requirement for the injection moulding process, therefore, is "defect-free”
Featuring tie-bar-less servo-hydraulic clamping and electric injection units, the injection moulding machines from the Engel e-victory series are predestined for precision applications with LSR. The electric Engel injection unit ensures high-precision injection. The excellent accessibility and the space available in the mould area are unique on this tie-bar-less injection moulding machine. Where multiple-cavity moulds are used, smaller machines than the mould would normally dictate can be used in many cases. This keeps both investment outlay and operating costs low. The moving platen follows the mould precisely while clamping force is being built up, which results in excellent platen parallelism. Patented force dividers ensure that the clamping force is distributed evenly over the entire platen face. Even for large multiple-cavity moulds, the cavities near the outer edge of the platen are kept closed with exactly the same clamping force as those nearer the centre.
The Engel easix articulated robot ensures optimum space utilisation on the automation side and also requires very little headroom. It connects the injection moulding machine with camera-based quality control and the discharge station and adapts flexibly if additional process units need to be retroactively integrated upstream or downstream of the injection moulding process.
It is in cases of batch fluctuations in the raw material, or environmental conditions, for example, due to weather conditions, that digitalisation comes into its own. Equipped with the iQ weight control smart assistance system from Engel's inject 4.0 portfolio, the injection moulding machine continuously analyses the injection profile and readjusts quality-relevant process parameters in the same cycle whenever deviations from the reference cycle occur.
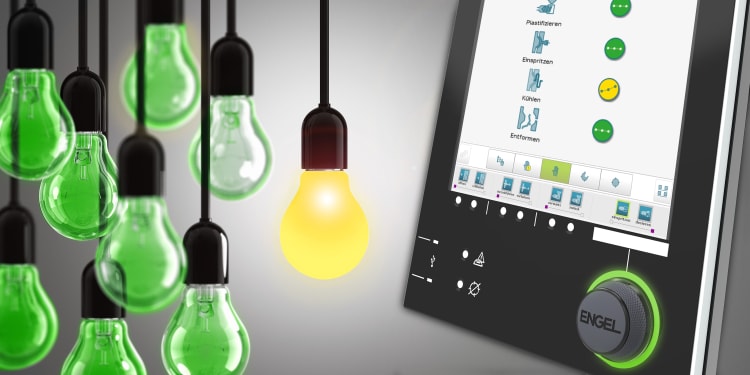
The Engel iQ process observer monitors quality by tracking hundreds of process parameters
Anticipate markets’ needs
In addition to the exhibits mentioned above, visitors will find further innovative applications that take into account the megatrends from the automotive, medical and packaging industries, as well as in the field of technical injection moulding. Anticipating the markets’ needs is a daily challenge. Engel meets this challenge together with customers and partners, because a culture of collaboration is the best way to achieve success.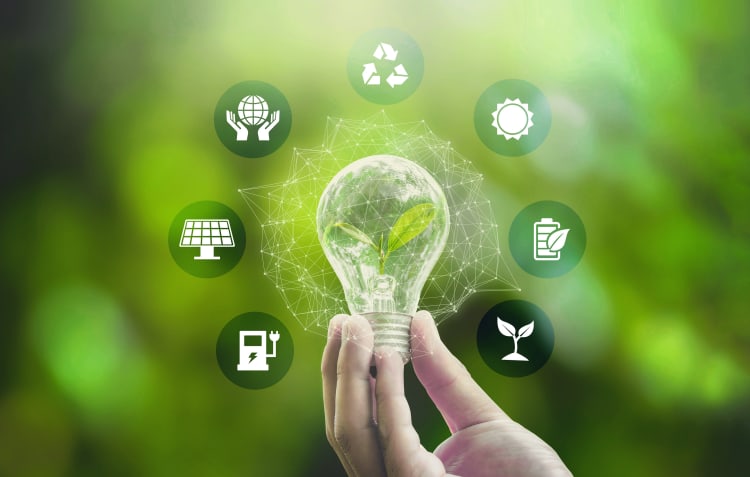
Energy and material savings are two key points of Engel’s sustainability strategy
Engel at Plast 2023 | Hall 24, stand C82