
Engel is set to welcome visitors to the smart factory at Elmia Polymer 2022, Scandinavia’s biggest trade fair for plastics and rubber processing, which takes place from May 10th to 13th in Jönköping, Sweden. The Austria-based injection moulding machine manufacturer and system solution provider, which also has a branch in Jönköping, will be presenting both new and established products from its inject 4.0 range. Themes addressed during the four-day trade event will include greater energy efficiency and the automation of injection moulding processes.
The Engel stand in Hall C will be devoted to the self-optimising injection moulding machine. By producing sample parts, Engel will vividly demonstrate how to exploit the potential for efficiency and quality that Industry 4.0 promises – fully and simply. The victory 460/120 injection moulding machine is equipped with smart assistance systems and networked for this purpose. The networking of production systems, the systematic utilisation of machine, process and production data and the deployment of smart assistance combine to enhance productivity, efficiency and quality in manufacturing while enabling processors to respond to ever-changing requirements with maximum flexibility.
Compensating for fluctuations to prevent rejects
At the trade fair, the injection moulding machine’s CC300 control unit will simulate fluctuations in the raw material and ambient conditions. Visitors to the fair will be able to watch live as the machine recognises deviations from specifications and automatically readjusts parameters, thereby reliably preventing rejects.
Three assistance systems from Engel’s iQ product range will be on show at the trade event. iQ weight control analyses the pressure profile during the injection process and compares measured values by means of a reference cycle. The injection profile, switchover point and the holding pressure profile are adjusted to the current conditions for every shot, which keeps the injected volume constant during the entire production run. At the same time, iQ clamp control calculates mould breathing in order to determine the ideal clamping force and adapt it automatically.
Thirdly, iQ flow control connects Engel e-temp temperature control units to the injection moulding machine via OPC UA. This makes it possible to regulate the rotational speed of the pumps in the temperature control units according to need. The result is significantly reduced energy consumption and the stability of the temperature control process is also enhanced. e flomo is capable of actively controlling the temperature difference in all individual circuits and automatically setting the required flow rate for each temperature control circuit.
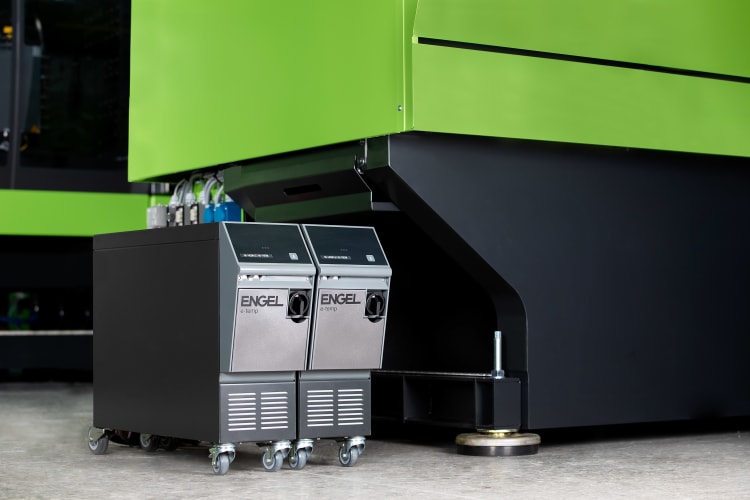
With iQ flow control, Engel has set a milestone on the road to secure data exchanges in the smart factory. e-temp temperature control units will be fully integrated into the CC300 control unit of the injection moulding machine via OPC UA.
Minimising energy losses
Thanks to the current generation of hydraulic injection units, the victory injection moulding machine presented at the event will achieve yet greater precision and process consistency. Control of temperature and pressure in the barrel contribute to this in equal measure. During development of the injection unit, special attention was paid to temperature control of the feed throat. The temperature control range was enlarged to safely rule out clumping in the feed zone and absorption of moisture across a wider range of materials. The new concept minimises energy losses both during heating and cooling of the feed through. The main contributor to better controllability of the pressures is the revised piston design.
The established Engel servohydraulic ecodrive comes as standard in all new victory machines. By preventing energy losses, ecodrive significantly cuts energy consumption while reducing carbon footprints.
Made-to-measure automation
Another focus of the Engel stand will be the automation of injection moulding processes. The victory 120 injection moulding machine is equipped with a viper 6 linear robot developed and produced by Engel – and the highly space-saving integration of the automation is striking. Thanks to its tie-bar-less clamping unit, the robot gripper can quickly reach the cavities of the mould from the side. The conveyor belt has also been integrated into the expanded safety gate of the machine.
As a supplier of integrated and automated system solutions, Engel can draw on a wide range of robots, conveyor belts and other peripheral components developed and manufactured in-house. Engel also incorporates solutions from partner companies into its overall concept. In northern Europe, for example, Engel collaborates with the 3Button Group, which is also based in Jönköping. At Elmia Polymer, 3Button will be presenting an automation exhibit of its own with an articulated robot at the Engel stand. By working with local partners, Engel can invariably develop precisely the right system solutions for specific injection moulding applications – solutions that are highly efficient and flexible.
Engel at Elmia Polymer 2022: Hall C, stand 4:20