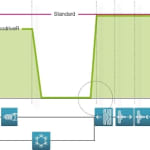
Rising energy prices and the demand for more sustainability often make manufacturing systems that have been used for many years seem even older. Engel's new retrofit solution ecodriveR is reasonably priced, can be fitted with little hassle and reduces the energy required by existing hydraulic injection moulding machines by up to 50%, increasing their cost-effectiveness significantly as a result.
Engel has been a leading developer of energy-efficient drive concepts for many years now. Engel set a new energy efficiency benchmark for all injection moulding machines, including hydraulic models, when it launched its servo-hydraulic system, ecodrive, in 2008. Consisting of a servomotor and a fixed displacement pump, this drive solution saves lost energy among other things. Without an energy saving option, lost energy builds up when a machine is idle and traditionally accounts for a large proportion of its total energy consumption.
Low cost, great effect
ecodriveR means hydraulic injection moulding machines with an asynchronous motor and electric-hydraulic variable capacity pumps (EHVs) can now be controlled according to demand as well. This is achieved through the installation of a frequency converter that adjusts the speed of the pump drive to the amount of energy required. ecodriveR is set using a simple interface of the machine control unit, Wolfgang Degwerth, head of Engel Austria's customer service division, states: "Since a machine's hydraulic system remains the same when it is retrofitted, ecodriveR allows us to adapt older injection moulding machines to the requirements of modern production companies quite quickly and at a relatively low cost. The first few uses have shown that, depending on the application, it can reduce the energy required by machines by up to 50% without affecting the cycle time, part quality or reproducibility standards."
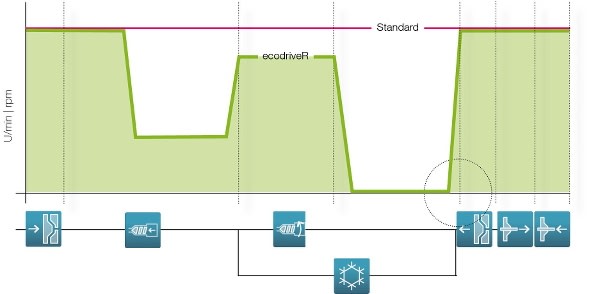