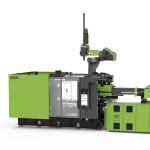
Precision, flexibility, efficiency – combine these success factors takes more than just reliable machines. Having a competitive edge relies on worry-free cooperation between the injection moulding machine and the process technology, automation and digitalisation.
ENGEL, the injection moulding machine manufacturer and system solution provider, is demonstrating what this can look like hands on at Plastimagen 2022 from 8 to 11 March in Mexico City with two sophisticated injection moulding applications.
One integrated process for unlimited design options
Flexibility and efficiency were the focus in the development of the reel-to-reel IMD application which ENGEL is presenting at its stand in Mexico City in collaboration with system partners Leonhard Kurz (Germany), Schöfer (Austria) and Isosport Verbundbauteile (Austria). To manufacture complex, three-dimensional sample parts, the duo 1060/350 injection moulding machine with an integrated viper 20 robot uses two process technologies at the same time: foilmelt and foammelt. foilmelt stands for flexibility more than anything else here. Different decorative foils are thermoformed, back-injected and punched from reel-to-reel in the mould in quick succession in a one-step process.
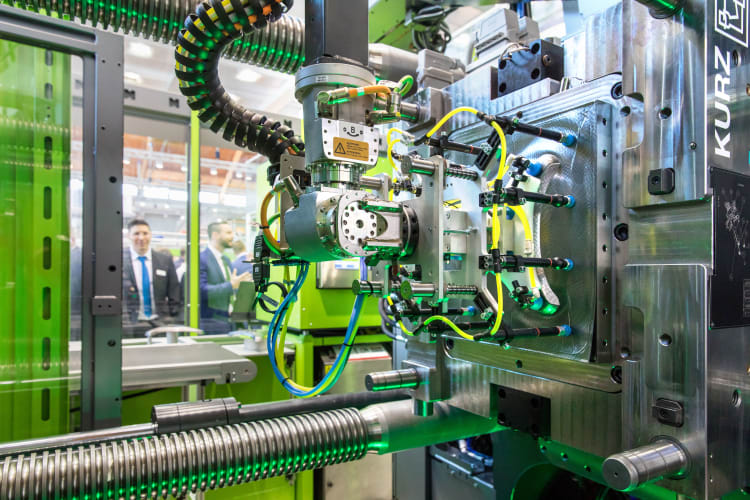
foammelt structural foam moulding – the MuCell physical foam injection process is used here – stands for the highest possible material and energy efficiency. In foamed parts, a porous core is embedded in a compact cover layer. This sandwich design reduces the use of material and correspondingly the weight of the parts. At the same time, the gas load reduces the viscosity of the molten plastics, which offers the ability to use smaller injection moulding machines in many applications as less clamp force is required.
The wide range of applications for the production-mature process combination is remarkable. It is suitable for visible components in the vehicle interior, in electronic devices, and for household appliances, among other things. Both multi-layer film systems with paint film surfaces and structured, back-lighting capable or open-pored systems such as wood, and also functionalised films with capacitive electronics, can be processed off the roll. To change the decor, the surface structure and the functionality, only the roll has to be changed, not the mould. Besides PP, ABS, PC or PC/ABS and recycled materials can be used for back injection.
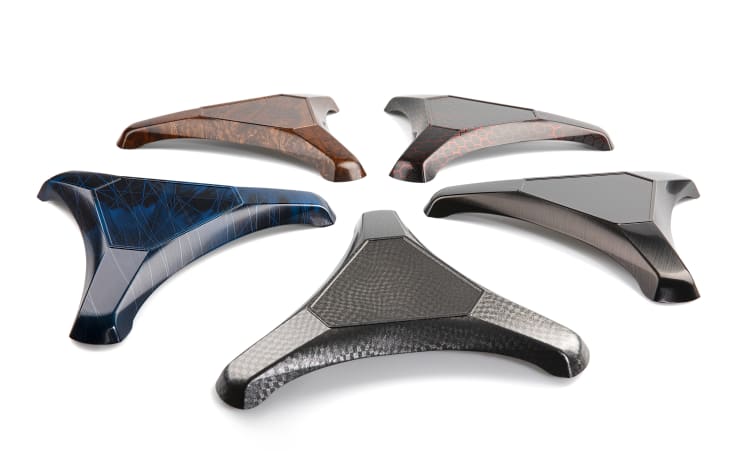