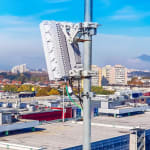
Shenzhen Xingshengdi New Materials Co., Ltd, a manufacturer of communication equipment, electronics and electrical appliances in China, has used BASF’s plastic additives to produce 5G base stations for major international telecommunications companies. With Tinuvin 360, the outdoor 5G base stations can withstand weathering and degradation by intense sunlight, thus maintaining stable service with extended life span.
The base station that uses radio waves to relay communications between the mobile device and the core network is commonly mounted outside a building. Usually, it is made of polycarbonate which undergoes various degradation reactions when exposed to sunlight and must therefore be light stabilized.
Tinuvin 360 is added to the polycarbonate resins during the production stage as it is particularly suitable for processing and weathering conditions where high loads, very low volatility and good compatibility are required. Low volatility reduces die build-up and allows longer running times, resulting in more stable processing, reduced production time and maintenance costs.
Also, Tinuvin 360 can achieve high UV (ultraviolet) screen performance in the final electronic casing: it absorbs UV light and releases the excess energy as heat. The additives used resemble those in sunscreen products, which protect skin from a UV attack.
''Tinuvin 360 creates value by optimizing the production process, thereby increasing productivity and profitability for our customers,'' said Hermann Althoff, Senior Vice President of BASF’s Performance Chemicals division in Asia Pacific. ''It also helps to create custom-formulated plastic appliances that are designed to be mechanically tougher and weather-resistant.''
''Previously such outdoor base stations were made of metal,'' said Dethew Xu, General Manager of Shenzhen Xingshengdi New Materials Co., Ltd. ''Making them available in small, lightweight plastic packages improves the size, weight, and power performance for a range of commercial applications, thus optimizing system performance at a competitive price.''
BASF conducts intensive research in its laboratories to stabilize plastics against UV radiation. Application testing takes place in specially equipped laboratories and application centers where chemists investigate the degradation mechanisms of plastic. The knowledge gained in this process flows directly into the development of hindered amine light stabilizers (HALS) and UV absorbers.
Tinuvin 360 has been tested under simulated environmental conditions in accelerated weathering devices according to the requirements of ISO 4892-2:2013. This international standard specifies the methods for exposing specimens to xenonarc light in the presence of moisture to reproduce the weathering effects (temperature and humidity) that occur when polymers are exposed in actual enduse environments to sunlight. Based on the data obtained from accelerated weathering, the durability to be expected for polymers in the different applications will be estimated.
Source: BASF