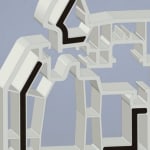
Ultradur simplifies production and cuts costs
The BASF plastic Ultradur is put to use in numerous industry applications in high-grade and highly stressed technical components. The material specially developed from an Ultradur blend reinforced with glass fibers offers profile manufacturers and window constructors numerous advantages. “Thanks to its simplified production and cost-effectiveness, our new Ultradur gives both profile manufacturers and window constructors a competitive edge in the marketplace,” says Dr. Kay Brockmüller, Project Manager Construction at BASF.Benefits for profile manufacturers and window constructors
An attractive feature for profile manufacturers is the possibility of co-extrusion with PVC. Highly rigid Ultradur binds with PVC and, in the right position, can replace conventional steel stiffeners in profiles. The co-extruded profile is weldable and undergoes the same downstream treatment as other profiles. The process also permits the best-possible reinforcement geometry for the profile in question.For window constructors, the production effort is reduced considerably, as all the steel-associated activities are eliminated. In the chain from purchase through to processing, several steps are omitted, thus avoiding the potential for error in steel handling at the same time. Handling - be it during the dyeing of the corners or installation in the building - is additionally simplified, as the profile reinforced with Ultradur is much lighter. A further positive feature for the ultimate customer, in addition to improved insulation performance, is that the profile shows high dimensional stability and virtually no tendency to shrink after installation.
Fast track to the mass-produced item
BASF offers profile manufacturers technical support with the development of new Ultradur profiles. Greiner Extrusion Group, the Austrian supplier of extrusion lines, tooling and complete production plants for profile extrusion, can deliver dependable series tooling for the co-extrusion of Ultradur with PVC at short notice. Leopold Weiermayer, Technical Manager at the Greiner Extrusion Group, sees huge potential in this: “With the expertise developed by Greiner for the necessary pronounced forward orientation of the fibers in the direction of extrusion combined with smooth running, we can offer tooling for this promising co-extrusion market.” BASF and the Greiner Extrusion Group are cooperating in this area to give customers rapid access to this technology, says Brockmüller: “This technology is highly exciting for many profile manufacturers and window constructors, but it calls for elaborate development steps in the tooling sector. Fortunately these have been taken by Greiner.”Source: BASF