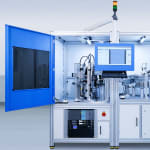
The plastics industry is facing radical changes: new regulations require a new approach to resources. At the same time, the advance of digitalization (and even the use of artificial intelligence) are developments that harbor enormous potential. At Fakuma 2023 in Friedrichshafen (Germany), the Kistler Group will show what smart process monitoring can already achieve today, and which trends are set to shape the industry's evolution in the coming years. Highlights at Kistler's booth A2-2302 in hall A2 include non-contact measuring sensors for the medtech sector, sensors for 3D printing, and also the AkvisIO production data solution - now expanded to offer far-reaching options for data analysis. Optical testing systems complete Kistler's portfolio for the plastics processing sector.
Intelligent process monitoring and optimization that can automatically detect deviations from the standard during the injection molding process, adjust parameters, and separate bad parts by itself: This scenario is already possible today if the right sensor technology is combined with appropriate hardware and software. At this year's Fakuma, Kistler will demonstrate what a complete solution of this sort can look like in action: two of the latest sensors for injection molding and 3D printing (Types 4004 and 9239B) will be featured. The KVC 821 automatic sorting and testing system on display at Kistler's booth represents the latest generation of optical inspection systems, while new versions of the firmware for ComoNeo and ComoScout illustrate the extended functionalities of these process monitoring systems. Kistler's Stasa QC Optimizer - with new features – is another highlight at Fakuma. This software optimizes the settings on the injection molding machine to ensure that products of the best possible quality are manufactured. Improvements to the Stasa QC Optimizer include a new user interface, extended functionalities, and intuitive handling.
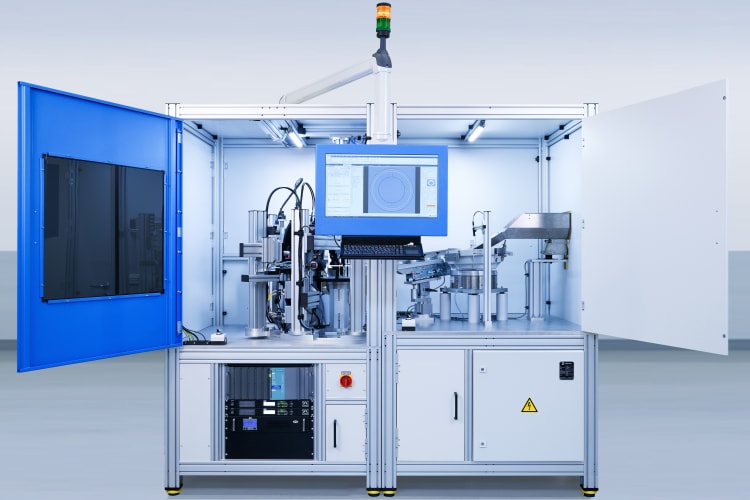
Automatic optical quality testing systems from Kistler check the dimensions, colors and surface characteristics of injection-molded products.
100-percent process control – even when using recycled materials
Complete process monitoring systems play a key part in achieving product quality and process efficiency. This is particularly true when companies make more use of recycled materials for their processes, and in higher proportions. "It's clear that the use of recycled materials in plastics manufacturing and processing will continue to increase," according to Felix Früh, Head of BU Plastics at Kistler. "But higher proportions of recycled material also have a negative impact on the stability of injection molding processes. The viscosity of the melt changes, for example. Process monitoring systems based on cavity pressure detect these fluctuations immediately and compensate for them continuously during the process. This allows users to guarantee homogeneous part quality even if the material characteristics vary."Miniature sensors for medtech applications, hot runners and 3D printing
The piezoelectric 9239B miniature longitudinal measuring pin – a sensor for no-contact cavity pressure measurement – will be center-stage at Fakuma. Available on the market since last year, this model takes up virtually no space when installed in the injection mold thanks to its diameter of only 2.5 mm. The 9239B uses a PiezoStar crystal grown specially by Kistler to measure the pressure-induced compression of the mold during the injection molding process – so it measures the cavity pressure indirectly. Unlike sensors that measure directly, the 9239B can be mounted between two and four millimeters behind the cavity wall, so it is protected from direct contact with the melt and its influences. The sensor offers another key benefit that is especially relevant for the medical sector: because of its position, it leaves no marks whatsoever on the manufactured plastic part. This means the longitudinal measuring pin is the solution of choice whenever flawless surfaces are required – on medical lenses, for example, or for automobile interiors. Another advantage: the pin's positioning means that it cannot become soiled or contaminated, so it is virtually maintenance-free.
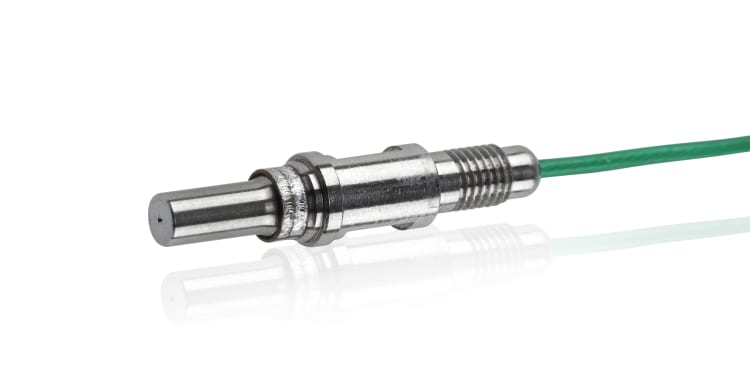
The 9239B miniature longitudinal measuring pin uses a PiezoStar crystal grown specially by Kistler to measure the pressure-induced compression of the mold during the injection molding process – so it measures the cavity pressure indirectly.
Kistler is also turning the spotlight on another miniature sensor: the 4004A melt pressure sensor. With a diameter of only 3 mm, it can be used directly in injection nozzles and small extruders. The 4004A withstands the extreme temperatures that prevail in these environments thanks to its wide operating and measuring range, which extends up to +350°C. The sensor is calibrated for two pressure ranges, so it can be used for injection molding applications (measuring range up to 2,500 bar) as well as additive manufacturing (measuring range up to 1,000 bar). This is a truly groundbreaking innovation for 3D printing applications: until now, the high temperatures involved have made it impossible for manufacturers to measure the melt pressure, so they have been unable to implement quality control while the process is actually running.
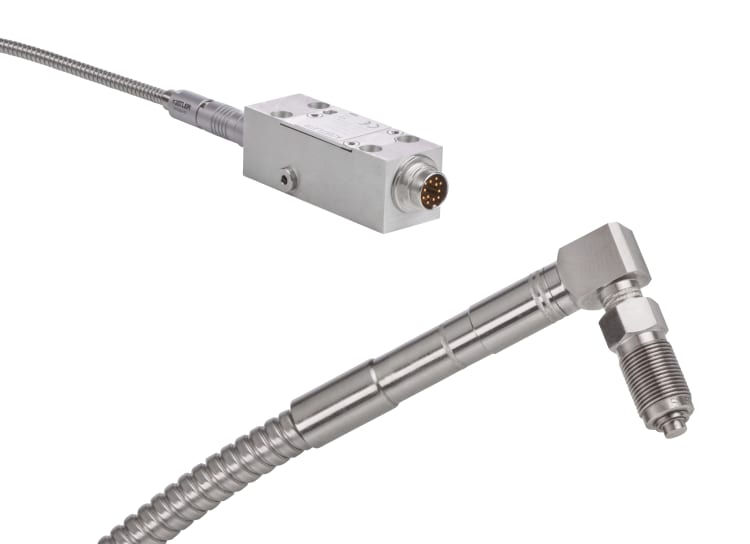
Thanks to its diameter of only 3 mm, the 4004A melt pressure sensor is especially suitable for use in injection nozzles and small extruders.