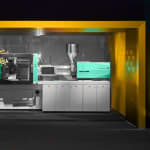
Arburg's expectations in Italy for the second half of the year are based on an increase in industrial production and rising investment. Arburg is responding to buyers' desire to save energy and the country's increased need for sustainability with its presence at Plast 2023 in Milan (stand C/D 61/62 in Hall 22). From 5 to 8 September Arburg will show the full range of technologies and will also present an interesting cooperation with Sverital in the field of silicone processing.
Arburg is meeting changing needs in Italy with future-oriented exhibits and has traditionally valued Plast as the key local trade fair for the plastics industry. "The market is moving towards electric machines and drives mainly for reasons of precision, energy efficiency and sustainability," observes Raffaele Abbruzzetti, Managing Director of Arburg Italy. "After the summer break, it's the right time for players in the plastics industry to have a fresh start, look around and find ideas that can make them more competitive."
For the first time: Allrounder 470 H processes solid silicon
Arburg is launching a new generation of machines with the Allrounder 470 H, which not only combines an electric clamping unit and hydraulic injection unit, but significantly reduces acquisition and operating costs as well as the carbon footprint. The machine presented in Milan will have a special configuration and will produce silicone parts from solid silicone for the first time. An ACH Turnmix feeder will be used as a peripheral device, while a linear robotic system Multilift Select 8 is depositing the parts on the conveyor belt.Complex: Allrounder 570 A produces flip-top closures
A typical packaging application is shown with an electric Allrounder 570 A Comfort producing from PP from Exxon Mobil flip-top closures for bottles in the beauty care sector. Italian mould manufacturer Giurgola Stampi is responsible for the complex mould. The Gestica control system has various assistance functions such as “aXw Control CycleAssist”,” aXw Control FillAssist”. The process can be conveniently managed via OPC UA interfaces to hot runners and the cooling system. "Because we don't just produce parts, but have the entire process under control thanks to our software solutions, we can make life easier for our customers and help them minimise quality problems," says Raffaele Abbruzzetti, summarising the benefits.Energy efficient: Injection compression moulding instead of thermoforming
The electric Allrounder 720 A Ultimate, an energy-efficient and sustainable alternative to thermoforming, will be celebrating its Italian premiere at the show. The machine, complete with 1300 injection unit, will be using injection compression moulding to produce environmentally friendly, thin-walled IML cups made from PP mono-material. A 4-cavity mould from Brink will be used to demonstrate the ICM process. For process monitoring, the mould is fitted with four compression path sensors. The plastic is biomass-balanced and ISCC-certified. Integrated into the production cell is a side-entry robot from Brink that inserts the labels, removes the finished cups and stacks them on a conveyor belt.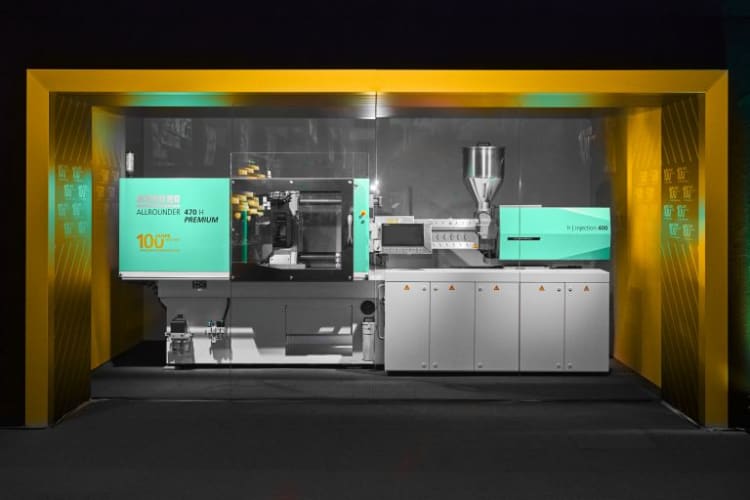
Arburg is launching a new generation of machines with the Allrounder 470 H milestone machine.