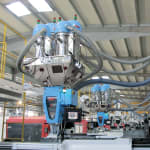
The transformation of plastic polymers involves a complex process with multiple steps to achieve a high-quality product from mechanical, aesthetic, and functional perspectives. One of the most critical stages is dosing, where the accurate blending of various raw materials, polymers, and additives is crucial.
The integration of advanced technologies and intelligent dosing solutions plays a key role in optimizing the production process, enabling higher levels of efficiency and quality. The use of sophisticated dosing systems contributes significantly to the overall success of the plastics industry, ensuring the production of finished products that meet high-quality and performance standards. In this context, the synergy between speed and precision in component mixing is essential to ensure an optimal result from both a technical and aesthetic point of view, while simultaneously minimizing production waste.
Moretto offers a wide and complete range of dosing solutions that includes volumetric and gravimetric dosing units. Within the gravimetric category, DGM Gravix stands out, currently undergoing a new phase of development marked by significant innovations that elevate precision and versatility standards to new heights. These innovations are geared towards ensuring even more precise and reliable dosing performance, reinforcing Moretto's constant commitment to delivering solutions that strive for excellence in the plastics industry.
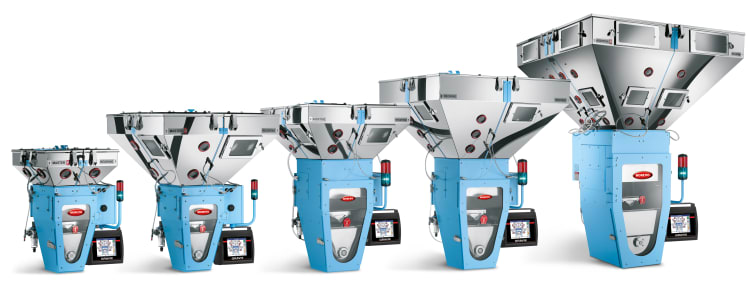
DGM Gravix is a gravimetric batch blender designed to blend plastic granules directly on the IMM for optimal efficiency. The high level of technology, combined with its quality performance, has enabled DGM Gravix to perfectly meet the needs of processors, with over 10,000 units sold since its launch on the market.
Dosing represents a fundamental phase in preparing mixtures comprising 3 to 6 components, with the primary goal of achieving a consistently high-quality final product. Throughout this process, it is essential to carefully manage various phenomena. Typically, one or two base materials are employed, alongside a colorant referred to as a masterbatch, serving an aesthetic function for the product. In addition to this, additives may be introduced, often in minor percentages, sometimes as low as a few grams.
During this process, a crucial element is weighing, which is carried out by load cells that detect and manage the constancy of dosing. However, the signal from the weighing cells is often subject to disturbances caused by vibrations, which can come from various sources. These vibrations interfere with the frequency generated by the weight sine wave, introducing random peaks that complicate signal interpretation.
Utilizing advanced signal analysis and filtering algorithms is essential for maintaining stability in weighing accuracy management, leveraging the capabilities of digital technology. This approach ensures consistent dosing accuracy, within a few grams, even over extended production periods. In developing these algorithms, the company's Research and Development department incorporated state-of-the-art software that harnesses the power of artificial intelligence (AI).
At the heart of the restyling
Recently, Moretto has made significant improvements to DGM Gravix by introducing technical solutions, in order to optimize its use and increase its performance thanks to the development of digitalization. These changes reinforce the quality of the product, ensuring extreme reliability.
The hopper design has been completely renewed to guarantee a regular granule flow, ensuring a constant dosing accuracy. This feature translates into greater operational reliability and the ability to maintain very high standards of accuracy.
The electrical cabinet has undergone meticulous design to enhance the ergonomics, engineering, and accessibility of control devices. Positioned strategically at the rear, it provides convenient access to all essential machine components, including electronics, weighing cells, and pneumatics.
The user interface has been upgraded with the introduction of a new 7-inch touch view, featuring an articulated arm that optimizes ergonomics during use. Visual communication is facilitated by a set of LEDs, illuminated in four distinct colours, clearly indicating the operational status of the machine.
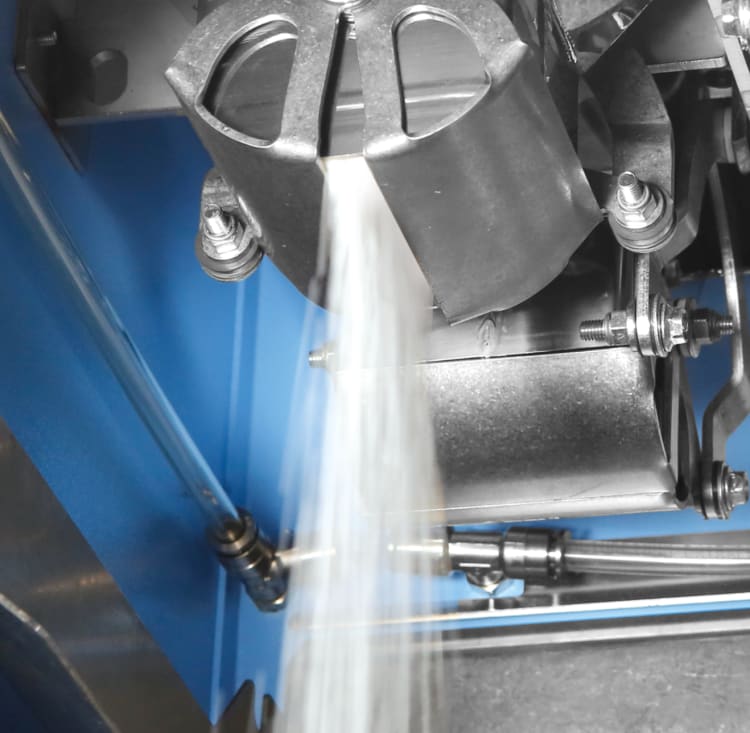